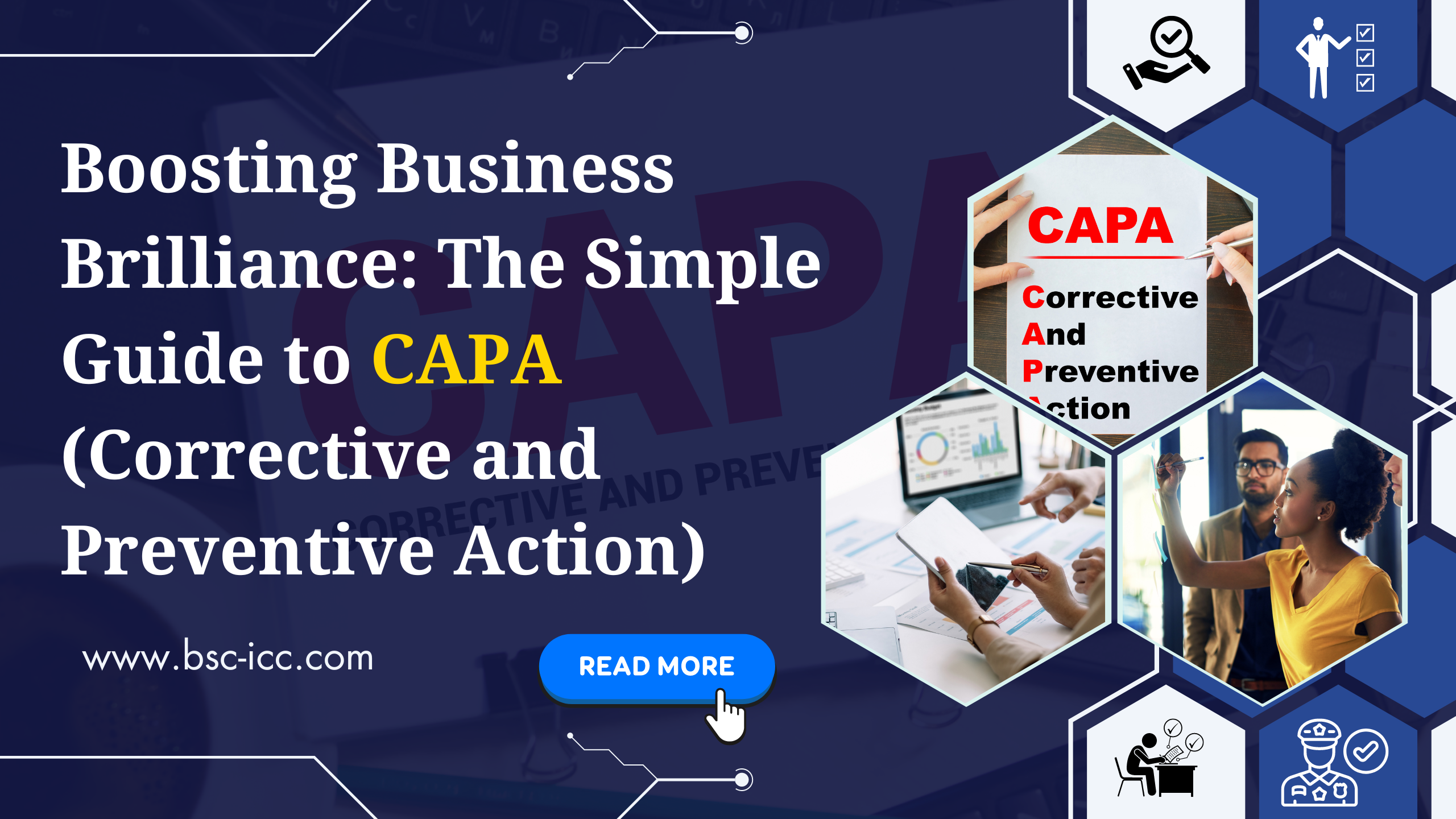
Corrective and Preventive Action Boosting Business Brilliance: The Simple Guide to CAPA (Corrective and Preventive Action)
Corrective and Preventive Action (CAPA) is a crucial aspect of quality management systems, offering companies a proactive approach to address issues and continuously improve processes. Here's how CAPA can benefit a company creatively:
1. Enhanced Productivity and Efficiency
- Identifying Process Bottlenecks: CAPA helps pinpoint areas of inefficiency or bottlenecks, allowing companies to streamline workflows and enhance productivity.
- Reducing Downtime: Timely corrective actions minimize downtime by addressing issues promptly, ensuring smooth operations and optimal resource utilization.
2. Improved Product Quality and Customer Satisfaction
- Root Cause Analysis: Through detailed root cause analysis, CAPA enables companies to address underlying issues affecting product quality, resulting in higher customer satisfaction and loyalty.
- Preventing Recurrence: By implementing preventive actions, companies can proactively prevent similar issues from arising in the future, fostering trust among customers.
3. Regulatory Compliance and Risk Mitigation
- Meeting Regulatory Standards: CAPA ensures compliance with industry regulations and standards by systematically addressing non-conformances and implementing corrective measures.
- Risk Management: Proactive identification and mitigation of risks minimize the likelihood of compliance violations, protecting the company's reputation and reducing financial liabilities.
4. Engaged Workforce and Continuous Improvement Culture
- Stakeholder Involvement: Involving employees in the CAPA process fosters a culture of ownership and accountability, encouraging proactive problem-solving and innovation.
- Learning Organization: CAPA promotes a learning culture where feedback and lessons learned from corrective actions are shared across departments, driving continuous improvement and organizational resilience.
Examples of CAPA Implementation
- Manufacturing Industry: A manufacturing company implements CAPA to address recurring defects in its production line. By analyzing root causes and implementing preventive measures such as enhanced training and equipment maintenance schedules, the company improves product quality and reduces waste.
- Healthcare Sector: A hospital implements CAPA to reduce patient wait times in the emergency department. Through process optimization and staff training initiatives, the hospital identifies inefficiencies and implements solutions to enhance patient flow and satisfaction.
- Automotive Industry: An automobile manufacturer utilizes CAPA to address safety recalls and product defects. By conducting thorough investigations and collaborating with suppliers, the company implements corrective actions such as design modifications and quality control enhancements to ensure product safety and compliance with industry standards.
In conclusion, CAPA serves as a catalyst for organizational excellence, empowering companies to proactively address challenges, drive innovation, and deliver superior products and services. By integrating CAPA into their quality management systems, companies can unlock new levels of performance and competitiveness in today's dynamic business landscape.